Budowa maszyn pneumatycznych to temat, który zyskuje na znaczeniu w różnych branżach przemysłowych. Maszyny te wykorzystują energię sprężonego powietrza do wykonywania pracy mechanicznej, co czyni je niezwykle efektywnymi i wszechstronnymi narzędziami. W procesie budowy takich maszyn kluczowe jest zrozumienie podstawowych zasad działania układów pneumatycznych, które obejmują kompresory, zawory, siłowniki oraz różnego rodzaju przewody. Kompresory są odpowiedzialne za sprężanie powietrza, które następnie trafia do zbiorników ciśnieniowych. Zawory regulują przepływ powietrza, a siłowniki przekształcają energię pneumatyczną w ruch mechaniczny. Dzięki zastosowaniu maszyn pneumatycznych możliwe jest osiągnięcie dużej siły przy stosunkowo niewielkim zużyciu energii.
Jakie są główne elementy budowy maszyn pneumatycznych
W kontekście budowy maszyn pneumatycznych istnieje kilka kluczowych elementów, które odgrywają istotną rolę w ich funkcjonowaniu. Po pierwsze, kompresor jest sercem całego systemu, ponieważ odpowiada za sprężanie powietrza do odpowiedniego ciśnienia. Istnieją różne typy kompresorów, w tym tłokowe, śrubowe i wirnikowe, które różnią się konstrukcją oraz zastosowaniem. Kolejnym ważnym elementem są zbiorniki ciśnieniowe, które przechowują sprężone powietrze i zapewniają jego dostępność w momencie potrzeby. Zawory kontrolują przepływ powietrza w systemie, umożliwiając precyzyjne sterowanie pracą maszyny. Siłowniki pneumatyczne przekształcają energię sprężonego powietrza w ruch liniowy lub obrotowy, co pozwala na wykonywanie różnorodnych zadań mechanicznych. Dodatkowo nie można zapomnieć o przewodach pneumatycznych, które transportują sprężone powietrze między poszczególnymi komponentami systemu.
Jakie są zalety i wady budowy maszyn pneumatycznych
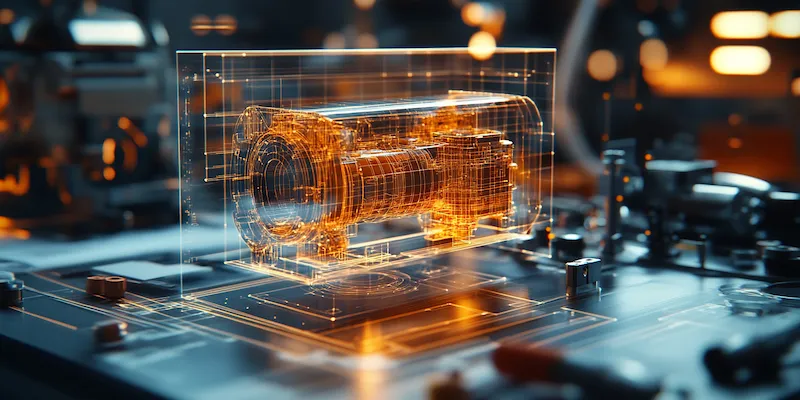
Budowa maszyn pneumatycznych
Budowa maszyn pneumatycznych wiąże się z wieloma zaletami oraz pewnymi ograniczeniami, które warto rozważyć przed podjęciem decyzji o ich zastosowaniu. Do głównych zalet należy niskie zużycie energii oraz możliwość uzyskania dużej siły przy stosunkowo niewielkich rozmiarach urządzeń. Ponadto maszyny pneumatyczne charakteryzują się dużą niezawodnością oraz prostotą obsługi, co sprawia, że są chętnie wykorzystywane w różnych gałęziach przemysłu. Ich konstrukcja pozwala na łatwe dostosowanie do zmieniających się potrzeb produkcyjnych oraz możliwość szybkiej wymiany części eksploatacyjnych. Z drugiej strony istnieją również pewne wady związane z budową maszyn pneumatycznych. Przede wszystkim wymagają one regularnej konserwacji oraz kontroli szczelności układów, aby uniknąć strat sprężonego powietrza. Dodatkowo ich wydajność może być ograniczona przez warunki otoczenia oraz jakość używanego powietrza.
Jakie zastosowania mają maszyny pneumatyczne w przemyśle
Maszyny pneumatyczne znajdują szerokie zastosowanie w różnych dziedzinach przemysłu dzięki swojej wszechstronności oraz efektywności działania. W przemyśle motoryzacyjnym są wykorzystywane do montażu komponentów oraz malowania pojazdów za pomocą pistoletów natryskowych działających na zasadzie sprężonego powietrza. W branży spożywczej maszyny te służą do pakowania produktów oraz transportu materiałów sypkich czy płynnych. W automatyce przemysłowej maszyny pneumatyczne odgrywają kluczową rolę w procesach montażowych oraz pakujących, gdzie precyzyjne sterowanie ruchem jest niezbędne dla zapewnienia wysokiej jakości produktów końcowych. Dodatkowo znajdują zastosowanie w robotyce przemysłowej, gdzie siłowniki pneumatyczne umożliwiają wykonywanie skomplikowanych ruchów manipulatorów. W sektorze budowlanym maszyny te są wykorzystywane do narzędzi ręcznych takich jak młoty udarowe czy wiertarki pneumatyczne, co znacznie ułatwia pracę i zwiększa jej efektywność.
Jakie są nowoczesne technologie w budowie maszyn pneumatycznych
W ostatnich latach budowa maszyn pneumatycznych zyskała na znaczeniu dzięki wprowadzeniu nowoczesnych technologii, które znacznie poprawiają ich wydajność oraz funkcjonalność. Jednym z kluczowych trendów jest zastosowanie inteligentnych systemów sterowania, które umożliwiają precyzyjne monitorowanie i regulację pracy maszyn. Dzięki zastosowaniu czujników oraz systemów automatyzacji, maszyny pneumatyczne mogą dostosowywać swoje działanie do zmieniających się warunków produkcyjnych, co pozwala na optymalizację procesów i zwiększenie efektywności. Kolejnym istotnym elementem jest rozwój materiałów stosowanych w budowie komponentów pneumatycznych. Nowoczesne tworzywa sztuczne oraz stopy metali o wysokiej wytrzymałości pozwalają na produkcję lżejszych i bardziej trwałych elementów, co przekłada się na dłuższą żywotność maszyn. Warto również zwrócić uwagę na rosnące znaczenie zrównoważonego rozwoju w kontekście budowy maszyn pneumatycznych. Producenci coraz częściej poszukują rozwiązań, które minimalizują zużycie energii oraz ograniczają emisję szkodliwych substancji do atmosfery.
Jakie są najczęstsze problemy w budowie maszyn pneumatycznych
Budowa maszyn pneumatycznych wiąże się z wieloma wyzwaniami, które mogą wpłynąć na ich efektywność oraz niezawodność. Jednym z najczęstszych problemów jest nieszczelność układów pneumatycznych, która prowadzi do strat sprężonego powietrza i obniżenia wydajności całego systemu. Nieszczelności mogą występować w różnych miejscach, takich jak połączenia przewodów, zawory czy siłowniki, dlatego regularna kontrola i konserwacja tych elementów są kluczowe dla utrzymania sprawności maszyny. Innym istotnym problemem jest niewłaściwe dobranie komponentów do konkretnego zastosowania. Wybór niewłaściwego typu kompresora czy siłownika może prowadzić do nieoptymalnej pracy maszyny oraz zwiększonego zużycia energii. Dodatkowo, jakość używanego powietrza ma ogromny wpływ na działanie systemu pneumatycznego. Zanieczyszczenia mogą powodować uszkodzenia elementów roboczych oraz obniżać efektywność działania całego układu.
Jakie są przyszłe kierunki rozwoju budowy maszyn pneumatycznych
Przyszłość budowy maszyn pneumatycznych zapowiada się bardzo obiecująco dzięki dynamicznemu rozwojowi technologii oraz rosnącemu zapotrzebowaniu na efektywne rozwiązania w przemyśle. Jednym z kluczowych kierunków rozwoju jest dalsza automatyzacja procesów produkcyjnych, co pozwoli na jeszcze większą precyzję i wydajność działania maszyn pneumatycznych. Wprowadzenie sztucznej inteligencji oraz algorytmów uczenia maszynowego umożliwi lepsze prognozowanie potrzeb produkcyjnych oraz optymalizację pracy systemu w czasie rzeczywistym. Kolejnym istotnym trendem jest rozwój technologii IoT (Internet of Things), która pozwala na zdalne monitorowanie stanu maszyn oraz ich parametrów pracy. Dzięki temu możliwe będzie szybsze wykrywanie potencjalnych awarii oraz planowanie konserwacji przed wystąpieniem problemu. Również rozwój materiałów kompozytowych oraz nanotechnologii przyczyni się do produkcji lżejszych i bardziej wytrzymałych komponentów, co wpłynie na ogólną efektywność systemów pneumatycznych.
Jakie są różnice między maszynami pneumatycznymi a hydraulicznymi
Maszyny pneumatyczne i hydrauliczne to dwa różne typy systemów mechanicznych, które mają swoje unikalne cechy oraz zastosowania. Główna różnica między nimi polega na medium roboczym – maszyny pneumatyczne wykorzystują sprężone powietrze jako źródło energii, podczas gdy maszyny hydrauliczne działają na zasadzie cieczy pod ciśnieniem. Dzięki temu maszyny pneumatyczne charakteryzują się mniejszą wagą oraz prostszą konstrukcją, co sprawia, że są łatwiejsze w obsłudze i konserwacji. Z drugiej strony maszyny hydrauliczne oferują znacznie większą siłę roboczą przy mniejszych rozmiarach urządzeń, co czyni je bardziej odpowiednimi do zastosowań wymagających dużych obciążeń. Warto również zauważyć, że maszyny pneumatyczne są bardziej elastyczne i mogą być łatwo dostosowane do zmieniających się potrzeb produkcyjnych, podczas gdy systemy hydrauliczne często wymagają bardziej skomplikowanej infrastruktury i instalacji.
Jakie są kluczowe aspekty bezpieczeństwa przy budowie maszyn pneumatycznych
Bezpieczeństwo jest jednym z najważniejszych aspektów przy budowie maszyn pneumatycznych, ponieważ niewłaściwe użytkowanie lub awarie mogą prowadzić do poważnych wypadków i uszkodzeń ciała. Kluczowym elementem zapewniającym bezpieczeństwo jest odpowiednie projektowanie układów pneumatycznych z uwzględnieniem norm i standardów branżowych. Ważne jest także stosowanie wysokiej jakości komponentów oraz regularna konserwacja urządzeń, aby uniknąć nieszczelności czy awarii mechanicznych. Pracownicy obsługujący maszyny pneumatyczne powinni być odpowiednio przeszkoleni w zakresie zasad bezpieczeństwa oraz procedur awaryjnych. Niezbędne jest również wyposażenie stanowisk pracy w odpowiednie środki ochrony osobistej takie jak rękawice czy okulary ochronne. Dodatkowo warto wdrożyć systemy monitorujące stan techniczny urządzeń oraz alarmowe sygnalizujące ewentualne zagrożenia związane z pracą układów pneumatycznych.
Jakie są koszty związane z budową maszyn pneumatycznych
Koszty związane z budową maszyn pneumatycznych mogą być różnorodne i zależą od wielu czynników takich jak skomplikowanie projektu, rodzaj zastosowanych komponentów czy wielkość produkcji. Na początku należy uwzględnić koszty zakupu sprzętu takiego jak kompresory, zbiorniki ciśnieniowe czy siłowniki pneumatyczne. Ceny tych elementów mogą znacznie różnić się w zależności od producenta oraz specyfikacji technicznych. Dodatkowo należy doliczyć koszty instalacji systemu oraz ewentualnych prac adaptacyjnych w zakładzie przemysłowym. Koszt eksploatacji również odgrywa istotną rolę – zużycie energii elektrycznej przez kompresory oraz koszty serwisowania powinny być brane pod uwagę przy planowaniu budżetu na maszyny pneumatyczne. Nie można zapominać o kosztach szkoleń dla pracowników obsługujących te urządzenia, ponieważ ich wiedza i umiejętności mają bezpośredni wpływ na efektywność działania całego systemu.