Destylator przemysłowy to urządzenie, które odgrywa kluczową rolę w procesach separacji substancji chemicznych. Jego działanie opiera się na różnicy temperatur wrzenia poszczególnych składników mieszaniny. W praktyce oznacza to, że podczas podgrzewania cieczy, substancje o niższej temperaturze wrzenia parują jako pierwsze, a następnie są skraplane i zbierane w osobnym pojemniku. W przemyśle chemicznym oraz petrochemicznym destylatory są wykorzystywane do oczyszczania surowców oraz produkcji wysokiej jakości produktów końcowych. Proces ten może być zautomatyzowany, co zwiększa efektywność i precyzję operacji. W zależności od zastosowania, destylatory mogą mieć różne konstrukcje, takie jak kolumnowe czy prostokątne, co wpływa na ich wydajność oraz jakość uzyskiwanych frakcji. Warto również zauważyć, że destylacja może być przeprowadzana w różnych warunkach ciśnienia, co pozwala na dalsze dostosowanie procesu do specyficznych potrzeb produkcyjnych.
Jakie są rodzaje destylatorów przemysłowych i ich zastosowania
W przemyśle istnieje wiele rodzajów destylatorów, które różnią się konstrukcją oraz przeznaczeniem. Najpopularniejsze z nich to destylatory kolumnowe, które charakteryzują się dużą efektywnością separacji dzięki zastosowaniu kolumny z wypełnieniem lub talerzami. Tego typu urządzenia są często wykorzystywane w przemyśle petrochemicznym do rozdzielania frakcji ropy naftowej. Innym rodzajem są destylatory prostokątne, które sprawdzają się w procesach wymagających mniejszych ilości surowców lub w laboratoriach badawczych. W przemyśle spożywczym popularne są także destylatory aromatów, które służą do produkcji esencji smakowych i zapachowych. Warto również wspomnieć o destylatorach próżniowych, które umożliwiają przeprowadzanie procesów w obniżonym ciśnieniu, co jest szczególnie istotne dla substancji wrażliwych na wysoką temperaturę.
Jakie są najważniejsze zalety stosowania destylatorów przemysłowych
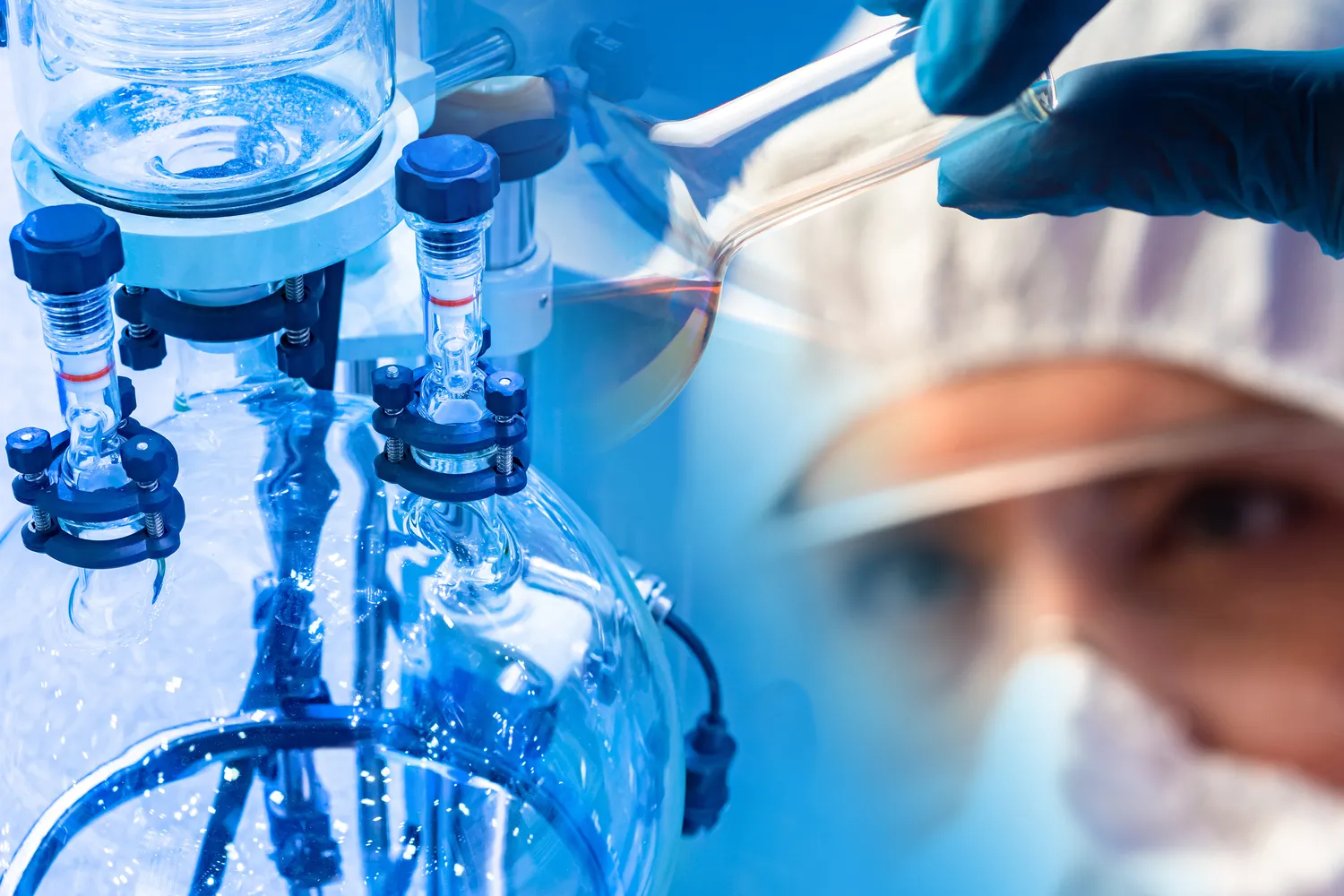
Destylator przemysłowy
Stosowanie destylatorów przemysłowych niesie ze sobą szereg korzyści, które mają kluczowe znaczenie dla efektywności procesów produkcyjnych. Przede wszystkim umożliwiają one uzyskanie wysokiej czystości produktów końcowych poprzez skuteczną separację składników mieszanin. Dzięki temu możliwe jest spełnienie rygorystycznych norm jakościowych obowiązujących w wielu branżach, takich jak farmaceutyczna czy spożywcza. Kolejną zaletą jest możliwość automatyzacji procesów destylacji, co prowadzi do zwiększenia wydajności oraz redukcji kosztów operacyjnych. Dodatkowo nowoczesne destylatory są wyposażone w zaawansowane systemy monitorowania i kontroli, co pozwala na bieżąco śledzić parametry procesu i dostosowywać je do zmieniających się warunków. Ważnym aspektem jest także elastyczność tych urządzeń – mogą być one dostosowane do różnych rodzajów surowców oraz wymagań produkcyjnych.
Jakie wyzwania stoją przed producentami destylatorów przemysłowych
Producenci destylatorów przemysłowych stają przed wieloma wyzwaniami związanymi z rosnącymi wymaganiami rynku oraz postępem technologicznym. Jednym z głównych problemów jest konieczność dostosowywania urządzeń do coraz bardziej rygorystycznych norm ekologicznych i bezpieczeństwa. W związku z tym producenci muszą inwestować w badania i rozwój nowych technologii oraz materiałów, które pozwolą na bardziej efektywne i bezpieczne procesy produkcyjne. Kolejnym wyzwaniem jest konkurencja na rynku globalnym, która zmusza firmy do ciągłego doskonalenia swoich produktów oraz oferowania innowacyjnych rozwiązań technologicznych. Również zmieniające się potrzeby klientów wymagają elastyczności i zdolności do szybkiego reagowania na nowe trendy i oczekiwania rynkowe. Dodatkowo producenci muszą dbać o utrzymanie wysokiej jakości swoich produktów przy jednoczesnej optymalizacji kosztów produkcji.
Jakie są kluczowe komponenty destylatora przemysłowego
Destylator przemysłowy składa się z kilku kluczowych komponentów, które współpracują ze sobą, aby zapewnić efektywny proces separacji. Na początku warto zwrócić uwagę na zbiornik destylacyjny, w którym umieszczana jest mieszanina do destylacji. Zbiornik ten jest podgrzewany, co powoduje parowanie składników o niższej temperaturze wrzenia. Kolejnym istotnym elementem jest kolumna destylacyjna, która może być wyposażona w talerze lub wypełnienie, co zwiększa powierzchnię kontaktu między parą a cieczą. Dzięki temu możliwe jest lepsze rozdzielenie frakcji. Po przejściu przez kolumnę para trafia do kondensatora, gdzie zostaje schłodzona i skroplona. Skroplony produkt zbierany jest w zbiorniku odbiorczym. Ważnym elementem jest także system kontroli temperatury i ciśnienia, który pozwala na precyzyjne monitorowanie procesu oraz dostosowywanie jego parametrów w czasie rzeczywistym. Oprócz tego wiele nowoczesnych destylatorów wyposażonych jest w systemy automatyzacji, które umożliwiają zdalne sterowanie procesem oraz zbieranie danych operacyjnych.
Jakie są najczęściej stosowane metody destylacji przemysłowej
W przemyśle chemicznym i petrochemicznym istnieje kilka metod destylacji, które są stosowane w zależności od rodzaju surowców oraz wymagań produkcyjnych. Najpopularniejszą metodą jest destylacja prosta, która polega na jednorazowym podgrzewaniu mieszaniny i oddzieleniu jej składników na podstawie różnicy temperatur wrzenia. Jest to metoda stosunkowo łatwa i tania, ale ma swoje ograniczenia w przypadku bardziej skomplikowanych mieszanin. Kolejną powszechnie stosowaną metodą jest destylacja frakcyjna, która wykorzystuje kolumnę destylacyjną do wielokrotnego skraplania i parowania składników, co pozwala na uzyskanie wyższej czystości produktów końcowych. W przypadku substancji wrażliwych na wysoką temperaturę stosuje się destylację próżniową, która obniża ciśnienie wewnętrzne układu i tym samym obniża temperaturę wrzenia składników. Istnieje także metoda destylacji azeotropowej, która wykorzystuje dodatkowe rozpuszczalniki do zmiany właściwości mieszaniny i umożliwienia separacji składników tworzących azeotrop.
Jakie są koszty związane z eksploatacją destylatora przemysłowego
Koszty eksploatacji destylatora przemysłowego mogą być znaczne i obejmują różne aspekty związane z jego użytkowaniem. Przede wszystkim należy uwzględnić koszty energii potrzebnej do podgrzewania surowców. W zależności od rodzaju wykorzystywanego paliwa lub źródła energii, te wydatki mogą znacząco wpłynąć na całkowity koszt operacyjny. Dodatkowo konieczne jest regularne serwisowanie i konserwacja urządzeń, co również generuje dodatkowe koszty. Warto również pamiętać o kosztach związanych z materiałami eksploatacyjnymi oraz ewentualnymi naprawami uszkodzonych komponentów. Koszty te mogą się różnić w zależności od intensywności użytkowania oraz wieku urządzenia. Kolejnym aspektem są koszty związane z przestrzeganiem norm ekologicznych i bezpieczeństwa pracy, które mogą wymagać inwestycji w dodatkowe technologie lub systemy monitorujące. Wreszcie nie można zapominać o kosztach związanych z zatrudnieniem wykwalifikowanego personelu obsługującego urządzenie oraz przeprowadzającego analizy jakości produktów końcowych.
Jakie innowacje technologiczne wpływają na rozwój destylatorów przemysłowych
W ostatnich latach branża przemysłowa doświadcza dynamicznych zmian związanych z innowacjami technologicznymi, które mają znaczący wpływ na rozwój destylatorów przemysłowych. Jednym z najważniejszych trendów jest automatyzacja procesów produkcyjnych, która pozwala na zwiększenie efektywności oraz redukcję błędów ludzkich. Nowoczesne systemy sterowania umożliwiają zdalne monitorowanie parametrów pracy urządzeń oraz ich optymalizację w czasie rzeczywistym. Kolejnym istotnym kierunkiem rozwoju są technologie związane z poprawą efektywności energetycznej procesów destylacyjnych. Inwestycje w nowoczesne materiały izolacyjne oraz systemy odzysku ciepła pozwalają na znaczne zmniejszenie zużycia energii podczas operacji destylacyjnych. Warto również wspomnieć o postępach w dziedzinie materiałów konstrukcyjnych, które zwiększają odporność urządzeń na korozję oraz wysokie temperatury, co przekłada się na dłuższą żywotność sprzętu. Również rozwój technologii analitycznych umożliwia dokładniejsze monitorowanie jakości produktów końcowych oraz szybsze reagowanie na ewentualne problemy podczas procesu produkcji.
Jakie są przyszłe kierunki rozwoju dla destylatorów przemysłowych
Przyszłość destylatorów przemysłowych rysuje się w jasnych barwach dzięki ciągłemu postępowi technologicznemu oraz rosnącym wymaganiom rynku. Jednym z kluczowych kierunków rozwoju będzie dalsza automatyzacja procesów produkcyjnych, co pozwoli na zwiększenie wydajności oraz redukcję kosztów operacyjnych. Producenci będą inwestować w inteligentne systemy zarządzania procesami, które będą mogły samodzielnie dostosowywać parametry pracy urządzeń do zmieniających się warunków rynkowych czy surowcowych. Kolejnym ważnym trendem będzie rosnąca potrzeba zgodności z normami ekologicznymi i zrównoważonego rozwoju, co skłoni producentów do poszukiwania bardziej ekologicznych rozwiązań technologicznych oraz materiałowych. W miarę jak świat staje się coraz bardziej świadomy problemów związanych z ochroną środowiska, branża musi dostosować swoje procesy do oczekiwań klientów i regulacji prawnych dotyczących emisji gazów cieplarnianych czy zużycia zasobów naturalnych. Również rozwój nowych materiałów konstrukcyjnych oraz technologii odzysku ciepła przyczyni się do poprawy efektywności energetycznej procesów destylacyjnych.