Połączenie dwóch kompresorów to zadanie, które może wydawać się skomplikowane, ale przy odpowiednim podejściu można je zrealizować bez większych trudności. Przede wszystkim warto zrozumieć, dlaczego chcemy połączyć dwa urządzenia. Często celem jest zwiększenie wydajności systemu, co pozwala na uzyskanie większego ciśnienia lub przepływu powietrza. Kluczowe jest również dobranie odpowiednich kompresorów, które będą ze sobą współpracować. Należy zwrócić uwagę na ich parametry techniczne, takie jak moc silnika, wydajność oraz ciśnienie robocze. W przypadku łączenia kompresorów, można zastosować różne metody, w tym połączenie równoległe lub szeregowe. Połączenie równoległe polega na tym, że oba kompresory pracują jednocześnie i dzielą obciążenie, co zwiększa wydajność systemu. Z kolei połączenie szeregowe umożliwia uzyskanie wyższego ciśnienia, ponieważ powietrze z jednego kompresora trafia do drugiego.
Jakie są najważniejsze kroki do połączenia kompresorów?
Aby skutecznie połączyć dwa kompresory, należy przejść przez kilka kluczowych kroków. Pierwszym z nich jest dokładne zaplanowanie całego procesu oraz zebranie niezbędnych materiałów i narzędzi. Warto sporządzić schemat instalacji, który pomoże w wizualizacji układu oraz ułatwi późniejsze prace montażowe. Następnie należy przygotować miejsce, w którym będą umieszczone kompresory. Powinno być ono dobrze wentylowane oraz dostosowane do wymagań technicznych urządzeń. Kolejnym krokiem jest podłączenie kompresorów do zasilania elektrycznego oraz wykonanie niezbędnych połączeń pneumatycznych. W przypadku połączenia równoległego należy zastosować odpowiednie rury i złączki, które umożliwią swobodny przepływ powietrza między urządzeniami. W przypadku połączenia szeregowego istotne jest prawidłowe ustawienie ciśnienia roboczego w każdym z kompresorów, aby uniknąć uszkodzeń sprzętu.
Jakie są korzyści z łączenia dwóch kompresorów?
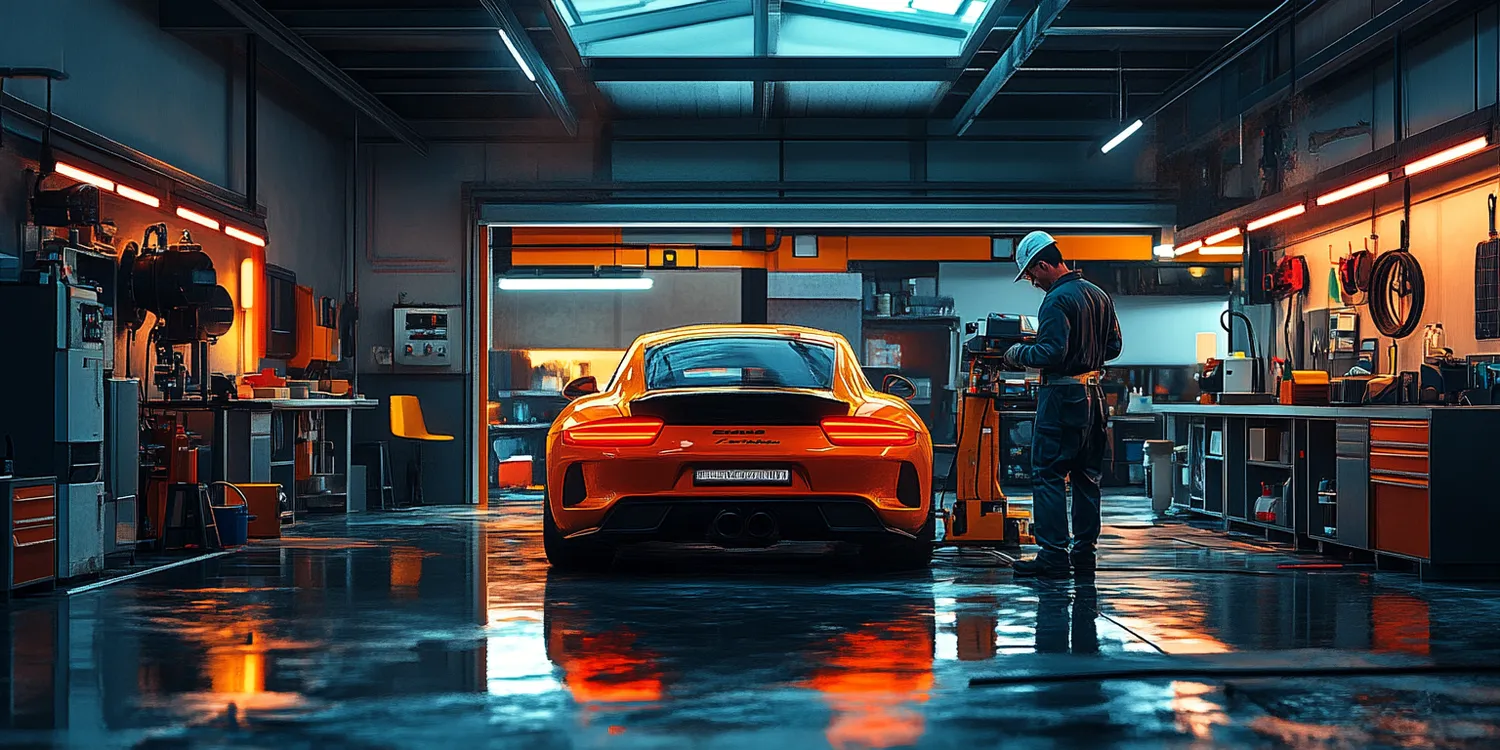
Jak połączyć dwa kompresory?
Łączenie dwóch kompresorów niesie ze sobą wiele korzyści, które mogą znacząco wpłynąć na efektywność pracy w różnych branżach. Przede wszystkim zwiększa to ogólną wydajność systemu pneumatycznego, co jest szczególnie istotne w przemyśle produkcyjnym czy budowlanym. Dzięki połączeniu dwóch urządzeń można uzyskać większy przepływ powietrza oraz wyższe ciśnienie robocze, co pozwala na szybsze wykonywanie prac oraz lepszą jakość końcowego produktu. Kolejną zaletą jest możliwość elastycznego dostosowania systemu do zmieniających się potrzeb produkcyjnych. W przypadku wzrostu zapotrzebowania na sprężone powietrze można uruchomić oba kompresory jednocześnie, co pozwoli na utrzymanie stabilności pracy maszyn i narzędzi pneumatycznych. Dodatkowo łączenie kompresorów może przyczynić się do oszczędności energii, ponieważ nowoczesne urządzenia często wyposażone są w systemy automatycznej regulacji pracy, które optymalizują zużycie energii w zależności od aktualnych potrzeb.
Jakie problemy mogą wystąpić podczas łączenia kompresorów?
Podczas łączenia dwóch kompresorów mogą wystąpić różnorodne problemy techniczne oraz operacyjne, które warto mieć na uwadze przed rozpoczęciem prac montażowych. Jednym z najczęstszych problemów jest niewłaściwe dobranie parametrów technicznych obu urządzeń. Jeśli jeden z kompresorów ma znacznie wyższą wydajność niż drugi, może to prowadzić do nierównomiernego obciążenia systemu oraz jego awarii. Kolejnym istotnym zagadnieniem jest kwestia instalacji pneumatycznej – niewłaściwie wykonane połączenia mogą prowadzić do wycieków powietrza oraz obniżenia efektywności całego układu. Dodatkowo nieodpowiednie ustawienie ciśnienia roboczego w poszczególnych kompresorach może skutkować ich uszkodzeniem lub nadmiernym zużyciem energii elektrycznej. Innym problemem mogą być trudności związane z synchronizacją pracy obu urządzeń – jeśli nie zostaną one odpowiednio zsynchronizowane, może to prowadzić do przestojów w produkcji oraz zwiększenia kosztów eksploatacji.
Jakie narzędzia i materiały są potrzebne do połączenia kompresorów?
Przy łączeniu dwóch kompresorów kluczowe jest posiadanie odpowiednich narzędzi oraz materiałów, które umożliwią sprawne i bezpieczne wykonanie całego procesu. Na początku warto zainwestować w zestaw podstawowych narzędzi, takich jak klucze płaskie, nasadowe oraz śrubokręty, które będą niezbędne do montażu i demontażu elementów instalacji. Dodatkowo przydatne będą narzędzia do cięcia rur oraz ich gięcia, co pozwoli na precyzyjne dopasowanie elementów pneumatycznych. W przypadku łączenia kompresorów istotne jest również posiadanie wysokiej jakości rur pneumatycznych, które będą odporne na wysokie ciśnienie oraz korozję. Rury te powinny być odpowiednio dobrane do średnicy wyjściowej z kompresorów oraz spełniać normy bezpieczeństwa. Warto również zaopatrzyć się w złączki, zawory oraz filtry powietrza, które są niezbędne do prawidłowego funkcjonowania systemu. Filtry powietrza pomogą w usunięciu zanieczyszczeń, co przedłuży żywotność kompresorów oraz zapewni lepszą jakość sprężonego powietrza.
Jakie są różnice między połączeniem równoległym a szeregowym kompresorów?
Połączenie kompresorów można zrealizować na dwa główne sposoby: równolegle lub szeregowo, a każda z tych metod ma swoje unikalne cechy oraz zastosowania. Połączenie równoległe polega na tym, że oba kompresory pracują jednocześnie i dzielą obciążenie. Taki układ jest szczególnie korzystny w sytuacjach, gdy potrzebujemy zwiększyć wydajność systemu, ale niekoniecznie wyższe ciśnienie. W przypadku połączenia równoległego oba urządzenia mogą działać niezależnie od siebie, co oznacza, że jeśli jeden z nich ulegnie awarii, drugi nadal będzie mógł zapewnić ciągłość pracy. Z drugiej strony połączenie szeregowe umożliwia uzyskanie wyższego ciśnienia sprężonego powietrza. W tym przypadku powietrze z jednego kompresora trafia do drugiego, co pozwala na zwiększenie ciśnienia roboczego w systemie. Jednakże takie rozwiązanie wymaga dokładnego dostosowania parametrów obu urządzeń oraz ich synchronizacji, aby uniknąć przeciążenia jednego z kompresorów. Warto również zauważyć, że połączenie szeregowe może prowadzić do większego zużycia energii elektrycznej, ponieważ oba urządzenia muszą pracować w pełnym zakresie swoich możliwości.
Jakie są zalecenia dotyczące konserwacji połączonych kompresorów?
Aby zapewnić długotrwałą i efektywną pracę połączonych kompresorów, niezwykle istotna jest regularna konserwacja tych urządzeń. Przede wszystkim należy zwrócić uwagę na regularną wymianę oleju oraz filtrów powietrza, co pozwoli na utrzymanie odpowiedniej jakości sprężonego powietrza oraz zmniejszenie ryzyka awarii. Warto ustalić harmonogram przeglądów technicznych, który będzie uwzględniał zarówno codzienne czynności konserwacyjne, jak i bardziej szczegółowe kontrole przeprowadzane co kilka miesięcy lub lat. Podczas przeglądów należy sprawdzić stan wszystkich elementów instalacji pneumatycznej – rury i złączki powinny być wolne od wycieków i uszkodzeń. Należy również monitorować ciśnienie robocze w systemie oraz porównywać je z wartościami nominalnymi podanymi przez producenta kompresorów. Ważnym aspektem konserwacji jest także kontrola poziomu hałasu emitowanego przez urządzenia – nadmierny hałas może świadczyć o problemach technicznych wymagających natychmiastowej interwencji.
Jakie zastosowania mają połączone kompresory w różnych branżach?
Połączone kompresory znajdują szerokie zastosowanie w różnych branżach przemysłowych i usługowych ze względu na swoją elastyczność oraz zdolność do dostosowywania się do zmieniających się potrzeb produkcyjnych. W przemyśle budowlanym często wykorzystuje się je do zasilania narzędzi pneumatycznych, takich jak młoty udarowe czy wkrętarki, co pozwala na efektywne wykonywanie prac budowlanych w krótszym czasie. W sektorze produkcyjnym połączone kompresory mogą być używane do obsługi maszyn montażowych oraz linii produkcyjnych wymagających dużego przepływu sprężonego powietrza. Dzięki zwiększonej wydajności systemu możliwe jest osiągnięcie lepszej efektywności produkcji oraz redukcja kosztów operacyjnych. W branży motoryzacyjnej połączone kompresory są wykorzystywane do malowania samochodów czy obsługi warsztatów naprawczych, gdzie wymagane jest stałe źródło sprężonego powietrza o odpowiednim ciśnieniu. Ponadto w sektorze medycznym sprężone powietrze jest niezbędne do działania wielu urządzeń diagnostycznych i terapeutycznych.
Jakie są koszty związane z łączeniem dwóch kompresorów?
Koszty związane z łączeniem dwóch kompresorów mogą się znacznie różnić w zależności od wielu czynników, takich jak rodzaj używanych urządzeń, materiały potrzebne do instalacji oraz ewentualne koszty robocizny związane z montażem systemu. Na początku warto zwrócić uwagę na cenę samych kompresorów – jeśli planujemy zakup nowych urządzeń, ich cena może być znaczącą częścią całkowitych wydatków. Dodatkowo należy uwzględnić koszty zakupu rur pneumatycznych, złączek oraz innych elementów instalacyjnych niezbędnych do prawidłowego funkcjonowania systemu. Koszty robocizny mogą być kolejnym istotnym elementem budżetu – jeśli zdecydujemy się na zatrudnienie specjalistycznej firmy zajmującej się montażem instalacji pneumatycznych, należy uwzględnić ich stawki godzinowe lub ryczałtowe wynagrodzenie za wykonane usługi. Nie można zapominać o kosztach eksploatacyjnych związanych z użytkowaniem połączonych kompresorów – zużycie energii elektrycznej może znacząco wpłynąć na miesięczne rachunki za prąd.